企业管理咨询中,关于如何有效持续推进5S管理咨询,解答如下:
咨询主题:如何有效持续推进5S管理
如何有效持续推行5S管理方法诀窍有三种:
1、5S管理现场巡视和高效跟进相集结合
执行力度和执行质量是5S管理现场巡视的两大内容
2、5S管理激励机制辅助,有效的激励方法对管理者提高工作效率是有益的。
3、5S现场管理奖惩机制铺垫,奖惩原则包括功奖过惩原则,奖惩及时原则,奖惩公开、公正原则、奖惩适度原则。
在中国,如何推行5S管理?怎么推行5S管理?
日本工业在许多方面达到世界先进水准,产品质量、效率、成本都属于领先地位,而日式生产管理值得效仿的地方都是5S:整理(SEIRI)整顿(SEITON)清扫(SEISO)清洁(SEIKETSU)素养(SHITSUKE)涵盖的内容。
中国改革开放20多年来,经济飞速发展,但也有不少企业在生产中纷纷落马。
中国现有企业,面临管理差距和管理滞后的挑战,而5S是最为基础的管理项目。
(一)从地理位置看中日两国差别
从地理位置上讲,中国是半内陆半沿海国家;而日本是个岛国,某种程度上就决定了两个国家人的生存方式的不同,中国人以农耕为主,日本人则以渔业为主,中国人30亩地一头牛,老婆娃娃热炕头,日本人只有一条渔船,靠捕鱼为生,这就形成了中日文化上的差别。
中国人喜欢积累,小而全,破家值万贯,而日本人全部家当就是一条船,他们的习惯是不断舍弃。
从以上分析可以看出,中国人搞5S的确困难,这也还是中国人和日本人之间存在的较大差距的原因。
5S文化是一种文化的侵略、碰撞、引进、照搬、交融,总之要变成自己的东西。
(二)中日不同习惯下的不同场面
中国许多工厂的现状:
1.物品堆放脏乱,良品、残品杂放——难保产品品质
2.工装夹具,随地置放——效率损失
3.机器设备保养不良——故障多
4.私人物品随意摆放,员工频繁走动——无次序
5.地面脏污,设施破旧,灯光灰暗——不安全易疲倦
6.物品无标识区分,误送误用——品质不佳
日本工厂:
据参观过日本工厂的人讲,第一感觉是清洁、有序,从办公场所到车间、仓库,从地面到工作台、天花板,都是亮亮堂堂,整洁无比。
员工工作节拍紧凑,士气高昂。
从工厂到家庭,到社会,到大家不妨想一想两国之间的差距。
(三)中日5S方法上的差别:
1.中国:热衷于口号、标语、文件的宣传,短暂的活动,很少结合日常具体工作开展。
2.日本:5S明确具体做法,简单有效,且融入到日常工作中,能实实在在提升。
(四)5S的认识误区
5S介绍到国内已有很长时间了,但有很多企业并不能按照5S的要求成功地坚持开展活动,甚至一些日资企业到中国后也对5S活动的开展一筹莫展。
为什么?原因就在于对5S产生种种认识上的误区:
1.我们已经做过5S了。
正确认识:5S永远是正在进行时,没有过去时和完成时。
2.5S就是把现场搞干净。
正确认识:打扫干净是一方面,更重要的是,让每个人养成良好的习惯。
3.5S只是工厂现场的事。
正确认识:5S是所有人的事。
4.5S可以包治百病。
正确认识:5S是管理及改善活动的基础,生产效率的提高,仅靠5S是不够的,还需要技术革新等。
5.5S活动看不到经济效益。
正确认识:5S作用是潜在的,长期坚持就会有作用,不可太多的急功近利。
6.工作太忙,没时间做5S。
正确认识:5S是工作的一部分,必须像对待工作一样对待5S。
7我们是搞技术的,做5S是浪费时间。
正确认识:5S对自身工作效率提升会起作用。
8.5S活动太形式化了,看不到实质内容。
正确认识:只有在形式上把5S内容固定下来,要求员工长期重复这些活动,才能养成习惯。
9.员工素质差,搞不好5S。
正确认识:是管理者自身的认识问题。
10.开展5S活动主要靠员工自发的活动,正确认识:5S需要全员参与,但不是放任自流,自上而下的推动十分必要。
l一旦把5S作为现场管理的“宗教”,被长期(虔诚地重复)坚持,5S活动就会为企业带来意想不到的效益。
5S是现场管理的基础,是TPM(全面生产管理)的前提,是TPM(全面品质管理)的第一步,也是ISO9000的有效保证。
更多如何推行5S管理,请访问理则5S管理。
理则图片展示:
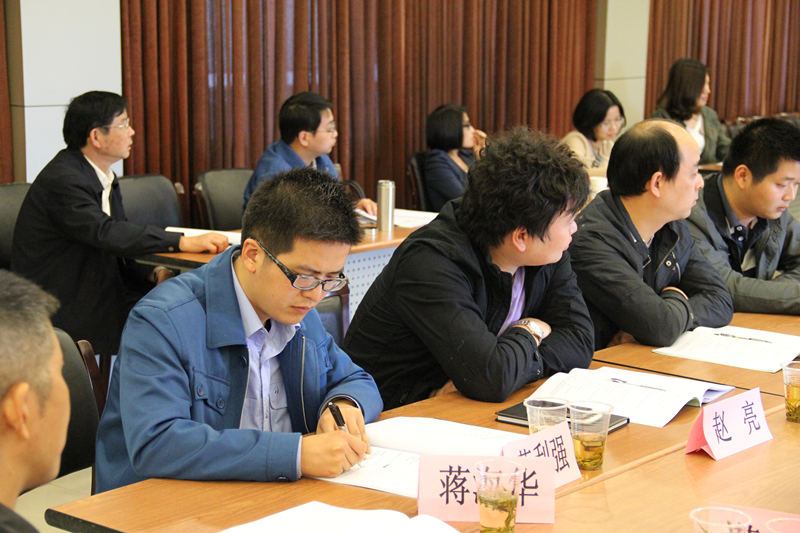
上海理则企业管理咨询有限公司可为您提供:
①5S管理|6S管理咨询培训、
②卓越班组长建设辅导培训、
③精益生产管理培训、
④企业TPM设备管理培训、
⑤精益六西格玛管理、
⑥生产车间现场管理制度建立、
⑦QC七大手法培训、
⑧质量管理体系咨询辅导。
…………
有关于如何有效持续推进5S管理、以及以上八条疑问,您也可以电询:18012685412或者网页右侧的在线客服